Nel settore del packaging, la qualità non è un valore aggiunto, ma un requisito fondamentale per garantire la sicurezza del prodotto e la soddisfazione del cliente finale. La crescente complessità delle linee produttive richiede soluzioni che vadano oltre il semplice controllo visivo, integrando tecnologie avanzate per una verifica sistematica e automatizzata.
Ercopac si distingue per la sua capacità di innovare in questo ambito, offrendo sistemi di controllo qualità brevettati che assicurano il massimo livello di affidabilità e precisione.
Un sistema avanzato per il monitoraggio in tempo reale
L’innovativo sistema di controllo qualità di Ercopac integra test di fasciatura in linea e strumenti di verifica della conformità delle palette, consentendo un monitoraggio continuo e in tempo reale.
Questa tecnologia permette di:
- Individuare difetti immediatamente: Eventuali anomalie nei carichi, nelle palette o nel film di fasciatura vengono rilevate tempestivamente.
- Prevenire sprechi: La capacità di intervenire immediatamente riduce gli scarti e ottimizza l’uso dei materiali.
- Garantire la conformità: Ogni pallet è sottoposto a verifiche che ne certificano la sicurezza e la stabilità, assicurando il rispetto degli standard richiesti
Grazie a questo sistema, le aziende possono contare su un controllo qualità dinamico e affidabile che minimizza i rischi di errori e inefficienze.
Sicurezza degli Operatori nel Controllo delle Palette Vuote
La sicurezza degli operatori è una priorità assoluta nei sistemi di controllo palette vuote sviluppati da Ercopac. Le tecnologie implementate sono progettate non solo per ridurre al minimo i rischi associati alla manipolazione manuale delle palette, ma anche per prevenire i pericoli connessi all’utilizzo di pallet non conformi nelle fasi successive del processo produttivo.
Un pallet difettoso, infatti, può ribaltarsi durante la movimentazione, con potenziali danni agli operatori in prossimità, oppure compromettere la stabilità del carico nelle fasi di pallettizzazione e fasciatura, generando il rischio di cadute dei prodotti e contaminazioni dell’area di stoccaggio.
Attraverso un controllo accurato e automatizzato, i sistemi Ercopac garantiscono la conformità dei pallet impiegati in linea, contribuendo in modo determinante a creare un ambiente di lavoro più sicuro e protetto.
Tra le caratteristiche principali dei sistemi Ercopac troviamo:
- Automazione completa dei controlli: Il sistema, basato sull’impiego di robot, consente di automatizzare integralmente le verifiche sulle palette vuote, evitando qualsiasi intervento manuale da parte degli operatori nelle fasi di prelievo e deposito. Questo approccio non solo ottimizza i tempi e riduce i rischi legati alla movimentazione, ma garantisce anche la massima affidabilità del processo di controllo, assicurando una gestione efficiente anche in presenza di palette non conformi.
- Sistemi di segnalazione avanzati: Sensori e dispositivi di allarme rilevano anomalie nelle palette, avvisando l’operatore solo in caso di necessità, evitando esposizioni a rischi inutili.
- Progettazione ergonomica: Le postazioni di controllo e intervento sono studiate per ridurre al minimo lo sforzo fisico degli operatori, prevenendo infortuni e lesioni da sforzi ripetuti. Inoltre, l’intero sistema è progettato per essere altamente accessibile e richiede una manutenzione ridotta, grazie all’utilizzo della robotica che ha permesso di minimizzare la componentistica meccanica.
- Protezione durante le fasi di scarto: Le palette non conformi vengono automaticamente scartate e convogliate in aree sicure, senza la necessità di movimentazione diretta da parte degli operatori.
Grazie a queste misure, i sistemi di controllo palette vuote di Ercopac non solo garantiscono un’elevata precisione operativa, ma offrono anche un livello superiore di sicurezza per gli operatori, contribuendo a creare un ambiente di lavoro più protetto e produttivo.
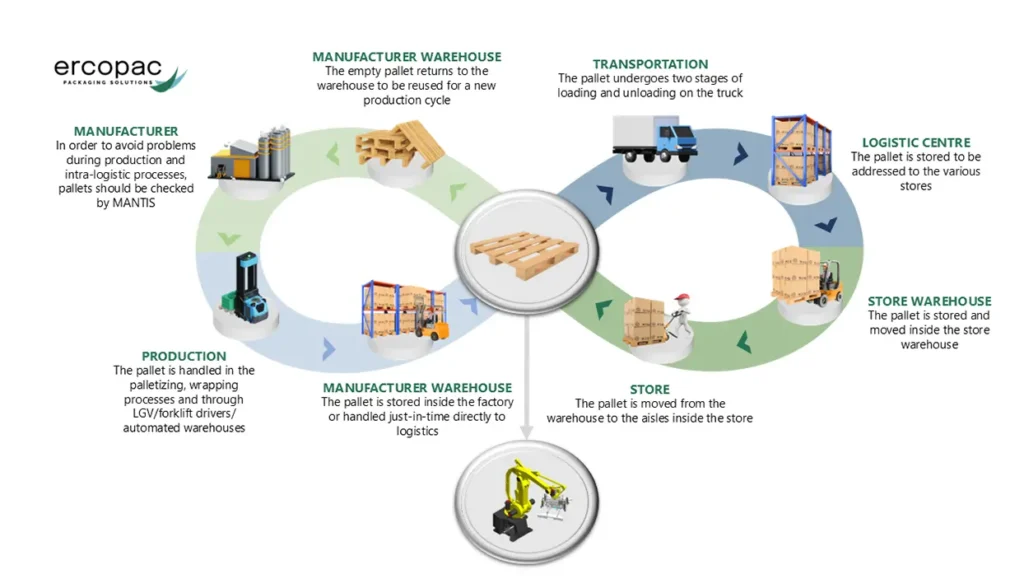
Il sistema automatico MANTIS per il controllo delle palette vuote rappresenta una delle soluzioni più avanzate sviluppate da Ercopac in ambito sicurezza e automazione. Come illustrato nello schema, ogni pallet attraversa una sequenza di stazioni dedicate che verificano l’integrità strutturale, la presenza di difetti (come assi pendenti o zoccoli danneggiati) e la corretta configurazione per l’utilizzo nei processi successivi.
Grazie alla gestione robotizzata, MANTIS garantisce un flusso continuo e affidabile: le palette conformi vengono automaticamente instradate verso l’area operativa, mentre quelle non conformi sono deviate in sicurezza in una stazione dedicata allo scarto, riducendo il rischio di errore umano e migliorando la qualità complessiva del processo.
Scopri di più sulla tecnologia MANTIS
Tecnologia brevettata per la stabilità del carico pallettizzato
Il cuore dell’innovazione Ercopac risiede nel suo sistema brevettato per la verifica della stabilità del carico palettizzato.
Attraverso sensori e algoritmi avanzati, la tecnologia analizza parametri chiave come:
- Tensione del film estensibile
- Adesione degli strati
- Resistenza ai movimenti durante il trasporto
Questo approccio scientifico alla stabilità non solo garantisce una fasciatura uniforme e sicura, ma consente anche di ottimizzare i consumi di film, migliorando la sostenibilità del processo produttivo.
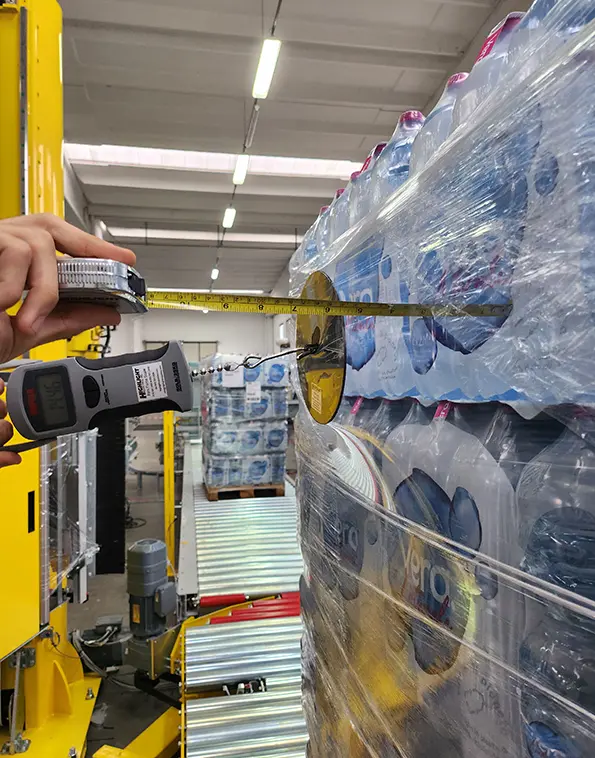
Modularità: adattarsi a ogni linea produttiva
Un elemento distintivo dei sistemi di controllo qualità Ercopac è la loro modularità, che permette una facile integrazione in linee produttive esistenti o nuove. Questa flessibilità consente alle aziende di adattarsi rapidamente ai cambiamenti del mercato senza interrompere la produzione.
La modularità si traduce in:
- Riduzione dei costi: Un unico sistema può essere utilizzato per diverse configurazioni produttive.
- Semplicità operativa: La scalabilità garantisce un’implementazione rapida e senza complessità.
- Future-proofing: Le soluzioni modulari sono facilmente aggiornabili per includere nuove tecnologie.
Vantaggi per il cliente finale
Un packaging di alta qualità non è solo un vantaggio per il produttore, ma anche una garanzia per il cliente finale.
Un controllo qualità rigoroso:
- Protegge l’integrità del prodotto: Evita danni durante il trasporto o lo stoccaggio.
- Aumenta la soddisfazione del cliente: Un prodotto ben confezionato trasmette professionalità e cura.
- Riduce i reclami: La conformità ai requisiti tecnici e normativi minimizza il rischio di contestazioni.
Il ruolo di Ercopac come partner strategico
Grazie alla sua esperienza e alla continua innovazione, Ercopac è un punto di riferimento per le aziende che cercano soluzioni avanzate per il controllo qualità nel packaging. La combinazione di tecnologie brevettate, sistemi modulari e un’assistenza tecnica dedicata rende Ercopac un partner affidabile per affrontare le sfide della qualità in un mercato in continua evoluzione.
Investire in un sistema di controllo qualità efficace non è solo una scelta strategica, ma una necessità per competere in un settore esigente come quello del packaging. Con Ercopac, le aziende possono contare su soluzioni che combinano precisione, flessibilità e sostenibilità, garantendo prodotti di altissima qualità e una gestione ottimale delle risorse.
Perché è importante il controllo qualità nel packaging?
Il controllo qualità è fondamentale per diverse ragioni:
- Sicurezza del prodotto: Previene contaminazioni, danni e alterazioni che potrebbero compromettere la salute dei consumatori (soprattutto nel settore alimentare e farmaceutico).
- Integrità del prodotto: Assicura che il prodotto arrivi al consumatore nelle condizioni ottimali, preservandone le caratteristiche qualitative.
- Conformità normativa: Garantisce il rispetto delle leggi e degli standard di settore (es. normative sull’imballaggio alimentare, farmaceutico, ecc.).
- Soddisfazione del cliente: Un packaging integro e funzionale contribuisce a una positiva esperienza del consumatore.
- Reputazione del marchio: Un packaging difettoso può danneggiare l’immagine aziendale e la fiducia dei consumatori.
- Riduzione degli sprechi e dei resi: Un controllo efficace previene difetti che porterebbero a scarti di produzione o a resi da parte dei clienti.
Quali sono i principali tipi di test che vengono effettuati sul packaging?
Esistono diversi tipi di test, a seconda del tipo di packaging e del prodotto contenuto:
- Test di resistenza meccanica: Verificano la resistenza a compressione, trazione, urto, perforazione, ecc.
- Test di tenuta: Verificano la capacità di sigillatura e la protezione da agenti esterni (umidità, ossigeno, ecc.).
- Test di migrazione: Verificano il rilascio di sostanze dal packaging al prodotto.
- Test di compatibilità: Verificano l’interazione tra il packaging e il prodotto.
- Test visivi: Verificano l’integrità estetica del packaging (difetti di stampa, etichettatura, ecc.).
- Test di stabilità del carico: verificano la stabilità del carico palettizzato e fasciato prima che sia trasportato o stoccato
Quali sono le normative di riferimento per il controllo qualità nel packaging?
Le normative variano a seconda del settore. Alcuni esempi includono:
- Regolamenti europei sui materiali a contatto con gli alimenti (es. Reg. CE 1935/2004 e Reg. CE 2023/2006).
- Normative ISO (es. ISO 22000 per la sicurezza alimentare, ISO 9001 per la qualità).
- Linee guida GMP (Good Manufacturing Practices) per il settore farmaceutico.
- Normative specifiche per il trasporto di merci pericolose (ADR).
Quali sono le conseguenze di un packaging difettoso?
Le conseguenze possono essere molteplici:
- Contaminazione del prodotto: Rischio per la salute dei consumatori.
- Deterioramento del prodotto: Perdita di qualità e valore commerciale.
- Resi e reclami da parte dei clienti: Costi aggiuntivi per l’azienda e danno all’immagine.
- Sanzioni legali: In caso di non conformità alle normative.
- Danni alla reputazione aziendale: Perdita di fiducia da parte dei consumatori.
Come si integra il controllo qualità con le altre fasi del processo produttivo?
Il controllo qualità dovrebbe essere integrato in tutte le fasi del processo, dalla progettazione del packaging alla produzione, al confezionamento, allo stoccaggio e al trasporto. Questo approccio, chiamato «qualità totale», permette di prevenire i difetti anziché correggerli a posteriori.
Come funziona il sistema per la verifica della stabilità delle palette?
Il sistema automatico di controllo palette garantisce – grazie ad un’accurata selezione preliminare – l’impiego di palette conformi alle esigenze del cliente e l’eliminazione di quelle non conformi.
Il sistema è strutturato in diverse stazioni che il pallet vuoto attraversa per essere controllato. Uno dei principali vantaggi derivanti dall’utilizzo del robot consiste nel fatto che già durante il prelievo e prima del deposito vengono fatti una serie di controlli; questo implica che, in caso di non conformità, il pallet vada automaticamente nella stazione degli scarti, e che altrimenti prosegua nel percorso di controllo.
Se non presenta difetti, viene messo nella stazione delle pile palette buone (suddiviso in 2/3 tipologie diverse), altrimenti sulla stazione pila palette scartate. È rara la possibilità che il pallet in questo ciclo si possa bloccare.
I principali controlli che vengono effettuati sono: integrità degli zoccoli, chiodi sporgenti, resistenza degli assi inferiori e superiori, asse pendente e vani inforcamento.
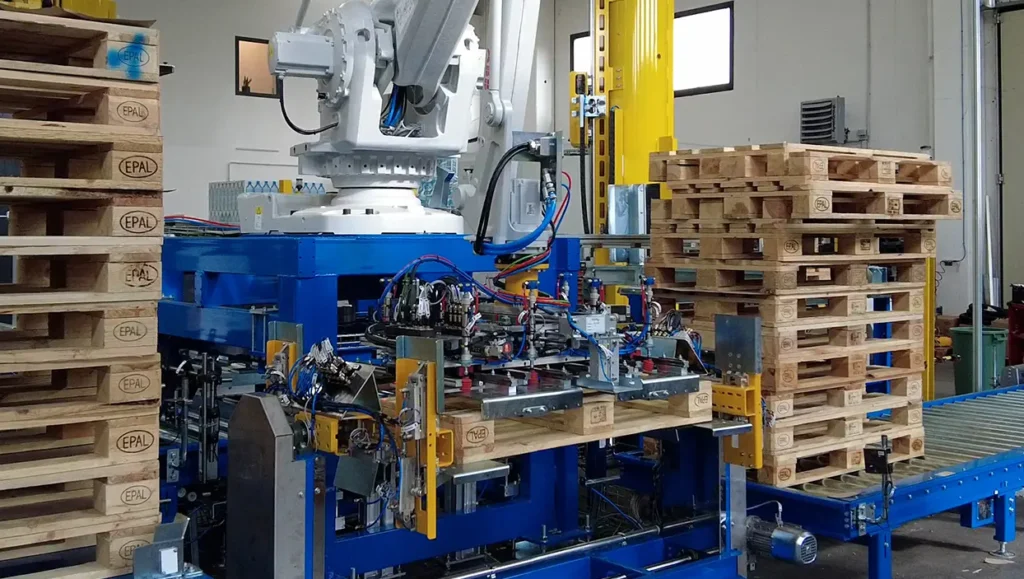
Quali parametri vengono misurati dal sistema di Ercopac?
La stazione di test della fasciatura in linea (brevettata da Ercopac) è progettata per simulare le condizioni che un carico su pallet, già avvolto con film protettivo, potrebbe affrontare durante il trasporto e lo stoccaggio. In pratica, serve a capire se l’imballaggio tiene bene anche quando il carico viene sottoposto a scossoni, inclinazioni o urti, come accade su camion, navi o altri mezzi.
Il sistema include una piattaforma che può inclinarsi in diverse direzioni: sia lungo la direzione in cui il carico «viaggia» (avanti e indietro), sia lateralmente. Questo fa sì che il pallet venga esposto a forze simili a quelle reali, causate da frenate, curve o movimenti bruschi, mettendo alla prova la resistenza dell’imballaggio.
Un grande vantaggio di questa stazione è che permette anche test manuali. Cioè, un operatore può intervenire direttamente per fare verifiche pratiche sul carico, usando strumenti già approvati e in linea con le norme del settore.
Per rendere il test ancora più realistico, la stazione ha anche dei blocchi – uno davanti e uno di lato – che servono per fermare il pallet mentre si muove. Quando il carico colpisce questi blocchi, si genera un impatto che può deformarlo o farlo spostare. Questo aiuta a vedere se il film protettivo è stato applicato nel modo giusto, cioè se riesce a tenere fermi i vari strati del carico senza farli cedere o spostare.
Infine, ci sono anche dei sensori che controllano la forma e le dimensioni del pallet prima, durante o dopo il test. Questi strumenti confrontano i dati rilevati con quelli memorizzati in precedenza, per vedere se ci sono variazioni oltre i limiti accettabili in base al tipo di pallet.
In sintesi, questa stazione serve a verificare quanto è stabile e sicuro un carico avvolto su pallet, prima che venga realmente spedito, aiutando così a prevenire danni e garantire trasporti più sicuri ed efficienti.
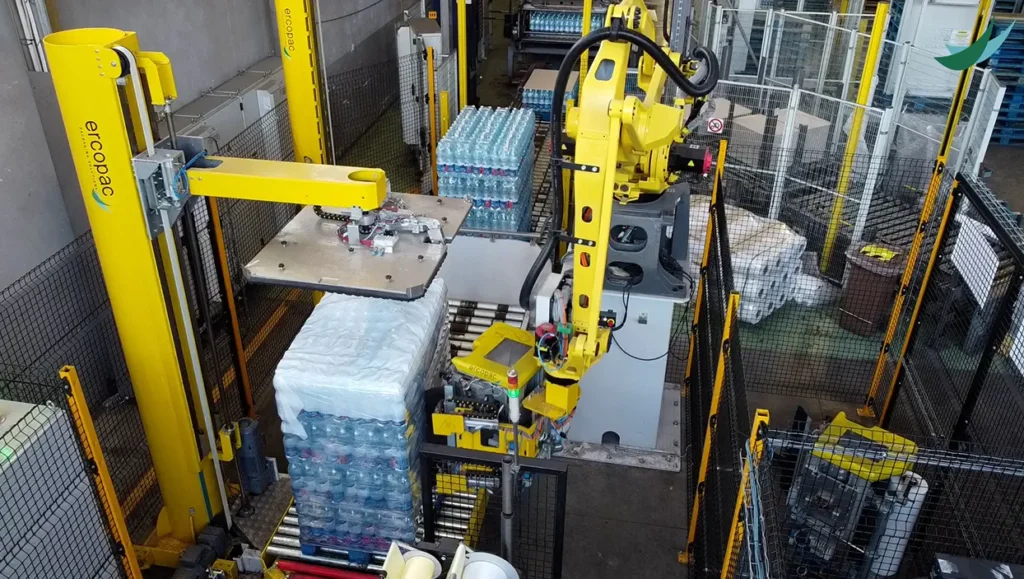
Quali sono i vantaggi specifici del sistema di monitoraggio in tempo reale di Ercopac?
Il sistema di monitoraggio in tempo reale di Ercopac offre vantaggi significativi che migliorano l’efficienza e la precisione dei processi produttivi. Tra questi, spiccano l’individuazione immediata dei difetti, che permette di intervenire tempestivamente per risolvere eventuali problemi, e la prevenzione degli sprechi, riducendo il consumo eccessivo di materiali. Inoltre, il sistema garantisce la conformità agli standard di qualità, minimizzando i rischi di errori e inefficienze.
Un ulteriore punto di forza è rappresentato dall’unità di controllo programmabile, che analizza i risultati dei test effettuati e li converte in istruzioni operative. Queste istruzioni vengono inviate automaticamente alla stazione di fasciatura, ottimizzando o adattando il tipo di avvolgimento necessario per garantire sempre un’operatività ottimale. Questa combinazione di precisione e automazione consente alle aziende di raggiungere elevati standard di qualità e produttività.
Il sistema di Ercopac è adatto a tutti i tipi di pallet e di carico?
I sistemi di Ercopac sono progettati per garantire la massima versatilità e adattabilità a diverse tipologie di pallet e carichi. Per quanto riguarda il controllo palette, i formati compatibili includono:
- EURO Pallet
- Mezzo Pallet
- Pallet GMA
- Pallet CHEP
- Mezzo Pallet CHEP
- Pallet Dusseldorf
Sul fronte dei test di fasciatura, invece, i sistemi Ercopac si adattano a una vasta gamma di carichi, come bottiglie, brick, lattine e rotoli di carta. Questi carichi possono essere contenuti in diverse configurazioni, tra cui cartoni, fardelli, sacchi e vassoi, garantendo sempre un’ottimale stabilità e sicurezza durante le fasi di stoccaggio e trasporto.
Ercopac offre assistenza tecnica e manutenzione per i suoi sistemi?
Ercopac garantisce un servizio di assistenza tecnica e manutenzione completo, pensato per soddisfare le esigenze specifiche di ogni cliente. L’offerta comprende manutenzioni programmate e straordinarie, assicurando che i sistemi funzionino sempre al massimo delle loro prestazioni. Gli interventi in loco sono accompagnati da report dettagliati e aggiornamenti al manuale di istruzioni d’uso e manutenzione, fornendo ai clienti tutte le informazioni necessarie per una gestione ottimale.
Per supportare l’efficienza operativa, Ercopac offre inoltre corsi di formazione personalizzati, disponibili sia online che in loco, con test di valutazione per garantire una comprensione approfondita delle tecnologie implementate. I contenuti e le modalità di erogazione sono adattabili alle necessità specifiche, concordati direttamente con il cliente.
Infine, l’assistenza tecnica è disponibile sia da remoto che in loco, con servizi di diagnostica avanzata per la risoluzione di problematiche hardware e software. Questo approccio integrato consente di mantenere i sistemi sempre efficienti, riducendo i tempi di inattività e garantendo un supporto continuo e affidabile.
Impatto sulla Sicurezza e la Qualità del Prodotto:
Il controllo qualità del packaging gioca un ruolo fondamentale nel garantire la sicurezza e la conservazione dei prodotti. Un packaging adeguato protegge i contenuti da agenti esterni come ossigeno, umidità, luce e microrganismi, rallentando il deterioramento e contribuendo a prolungarne la shelf-life. Tuttavia, un packaging difettoso può avere conseguenze gravi, permettendo la contaminazione da batteri, muffe o sostanze nocive, con rischi significativi per la salute dei consumatori.
Oltre alla protezione, il controllo qualità contribuisce anche a prevenire la contraffazione attraverso l’implementazione di elementi di sicurezza come ologrammi, microscritture, inchiostri speciali e sistemi di tracciabilità. Questi strumenti offrono una maggiore garanzia di autenticità e trasparenza lungo tutta la supply chain.
Le best practice per il controllo qualità del packaging variano in base al settore, ma includono il rispetto rigoroso delle normative specifiche, la validazione dei processi di confezionamento, il monitoraggio costante dei parametri critici, la formazione continua del personale e l’utilizzo di tecnologie avanzate. Questi approcci garantiscono standard elevati nei settori più critici, come quello farmaceutico, alimentare e industriale, dove la qualità del packaging è strettamente legata alla sicurezza e alla soddisfazione del cliente finale.