In recent years, industrial robotics has stopped being a futuristic concept and has become an established reality in many manufacturing sectors. From automotive to packaging, from food to logistics, the integration of robotic systems is redefining production dynamics, improving quality, optimizing time and reducing waste.
But the transition to automation is not without its challenges. Implementing robotics means investing in new technologies, rethinking processes and redefining the role of humans in industrial production. In order for this transition to bring value to businesses, it is essential to have a thorough understanding of its benefits and critical issues.
Ercopac, with its expertise in integrating robotic end-of-line systems, explores the potential of automation, analyzing new and emerging technologies and the impact robotics will have on the future of businesses.
Robotics and productivity: benefits for businesses
Increased operational efficiency
One of the main benefits of automation is the ability to operate continuously and repeatably, ensuring faster production cycles and greater stability in operations. In fact, industrial robotswork without interruption and maintain consistent quality standards, reducing the risk of errors and production waste.
Robotics in palletizing: operational efficiency and low maintenance
In the context of industrial robotics, palletizing has also benefited significantly from the integration of advanced solutions. The robotic palletizing systems employed by Ercopac stand out for their precision andoperational efficiency, thanks to a design that minimizes wear-prone components.
This results in a high Mean Time Between Failures ( MTBF ), which significantly reduces routine and extraordinary maintenance costs. In addition, configuration flexibility allows adaptation to different formats and load patterns, making these solutions particularly suitable for changing production environments.
Also in the automated wrapping systems robots optimize the use of stretch film, ensuring precise and efficient wrapping with less material consumption. This translates into cost savings and environmental sustainability.
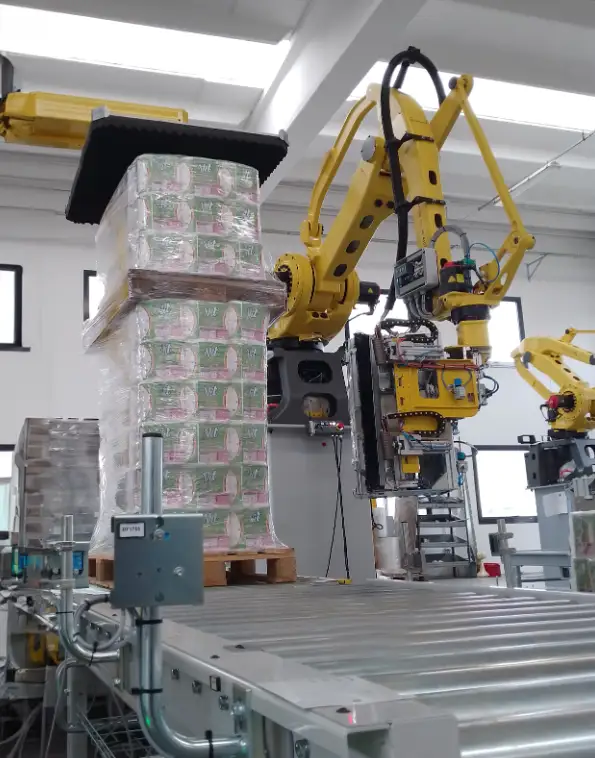
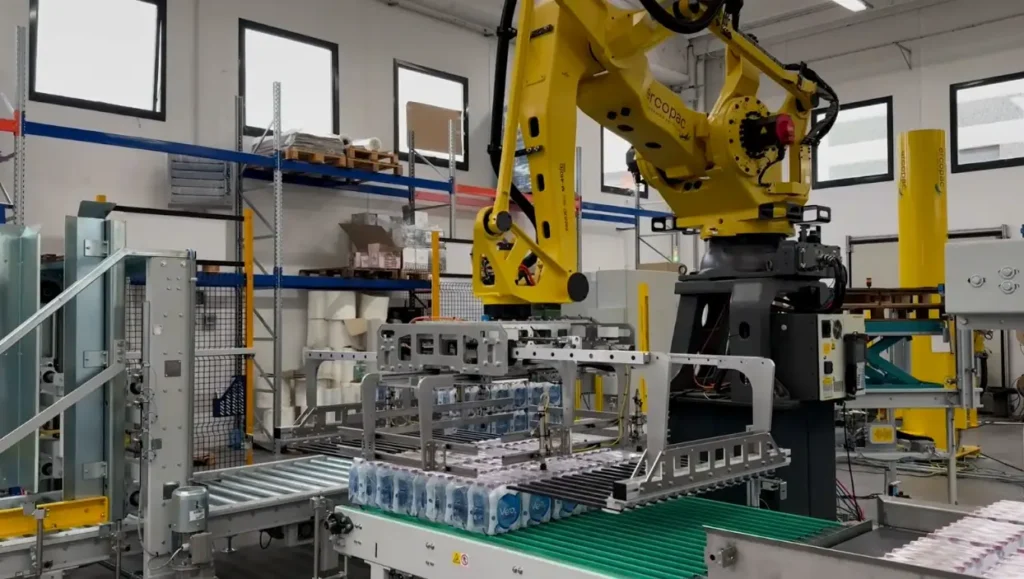
Occupational safety and risk reduction
Another crucial aspect of automation is security. Robots eliminate the need for manual handling of heavy loads, reducing the risk of injury and improving line ergonomics.
Industrial robotics allows dangerous or repetitive processes to be automated, reducing the risk of workplace accidents. Theintegration of robots into complex operations can not only increase efficiency, but also improve safety for operators, contributing to overall line ergonomics and freeing people from potentially harmful or exhausting tasks.
With the introduction of cobots (collaborative robots), production systems can now be configured to work alongside operators, supporting them in repetitive tasks and providing a safer working environment.
Cost optimization
Although the initial investment in automation can be significant, in the long run operating costs are reduced. The use of robots makes it possible to:
- Minimizing material waste
- Reduce downtime with predictive maintenance
- Decrease the need for revamping and quality control
The integration of robotics into production lines does not replace human labor, but redefines roles, paving the way for new professional skills in monitoring and managing automated systems.
The challenges of automation: between cost and flexibility
Initial investment and economic return
The adoption of industrial robots requirescareful financial planning. For many companies, especially small and medium-sized ones, the initial cost can be an obstacle. However, with the right implementation strategies and an accurate assessment of ROI, the investment can become a competitive advantage in the long run.
The adoption of an Ercopac robotic line represents a strategic investment oriented toward efficiency in the long run. The automated solutions developed by the company make it possible to significantly reduce energy consumption and mechanical maintenance costs. In addition, the complete integration of the systems makes it possible to plan a single annual routine maintenance operation for the entire line, minimizing downtime and maximizing productivity.
Adaptability to changes in production
While robots improve efficiency, they also require specific configurations for each type of production. A change in product specifications may require software and hardware upgrades, resulting in reconfiguration costs. However, emerging technologies, such as computer vision and machine learning, are making robots smarter and more adaptable, reducing the need for frequent reconfigurations.
Emerging technologies: the future of industrial robotics
Artificial Intelligence and Machine Learning
AI and Machine Learning are transforming industrial robotics, enabling robots to learn from data and autonomously optimize production processes. A concrete example is predictive maintenance systems, which analyze data in real time and prevent failures, optimizing productivity and reducing downtime.
Ercopac is also moving in this direction, constantly investing in intelligent solutions: one of the latest patents filed concerns an innovative in-line wrapping test system, which can perform real-time film quality checks and automatically suggest the most suitable wrapping recipes based on the products handled.
Collaborative Robotics (Cobot)
Cobots are designed to work in synergy with operators, offering greater flexibility than traditional robots. They are particularly useful in industries with variable production and high product customization.
Machine vision and advanced automation
With machine vision systems, robots can perform automatic quality checks, recognize shapes and sizes, and even detect anomalies in real time.
In packaging and packing systems, this allows for more accurate control, reducing errors and optimizing material management.
A concrete example is the robotic pallet control system MANTIS developed by Ercopac, which integrates mechanical and optical controls to ensure full pallet compliance. Using machine vision, MANTIS can detect critical issues such as sloping axes or irregularities in the forging compartments in real time, thus ensuring high operational reliability.
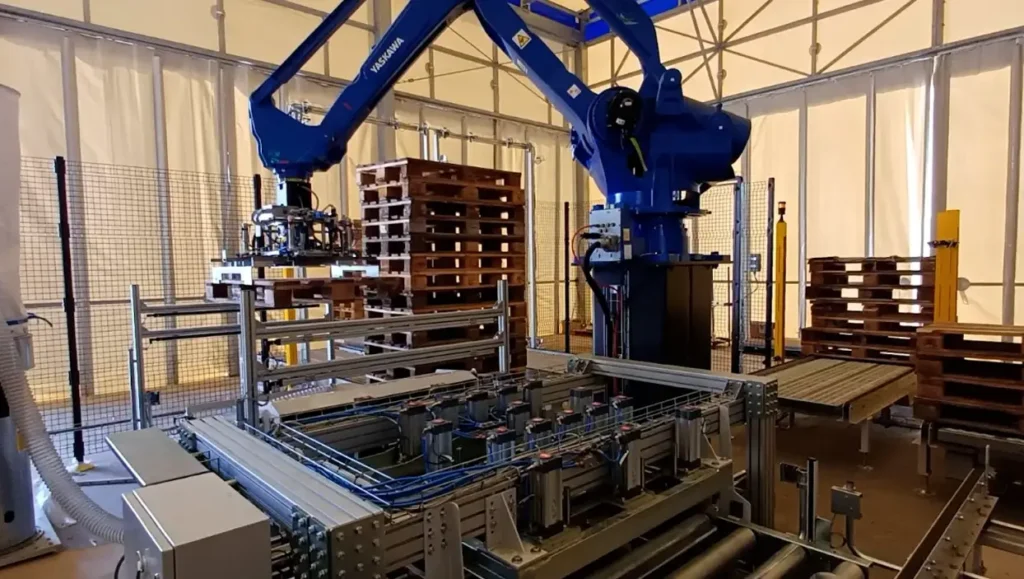
Sustainability and automation: a winning combination
Industrial robotics is not only synonymous with productivity, but can also play a key role in sustainability. Automation makes it possible to:
- Reducing material consumption through dosing systems and intelligent use of resources
- Optimize energy consumption with next-generation robots designed to reduce waste
- Foster the circular economy through solutions for recycling and responsible management of industrial waste
A sustainable approach to automation not only improves a company’s environmental impact, but also becomes a competitive advantage in a market increasingly oriented toward eco-friendly practices. Robotic wrappers also fit into this direction. SPIDER from Ercopac, designed to optimize the distribution of plastic film over the product, significantly reducing its consumption. These systems also support the use of high-performance recycled film, making a concrete contribution to the transition to a more efficient and sustainable production model.
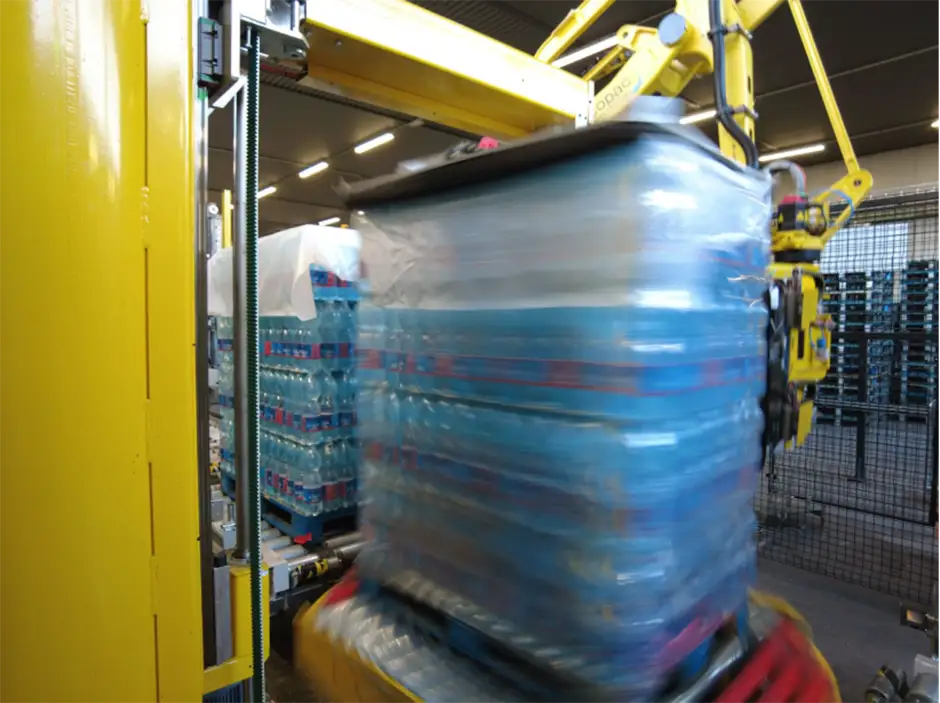
Toward a more humane robotics
The integration of industrial robotics is not a threat to human labor, but a transformation that requires awareness and strategy. The future of manufacturing will not be entirely automated, but characterized by intelligent collaboration between humans and machines.
Ercopac accompanies companies on this journey, offering tailored end-of-line solutions from wrapping to palletizing to advanced pallet control systems.
If robotics is the future of manufacturing, the real competitive advantage will come from those who can adopt it intelligently, integrating it into their production model without losing sight of the human element.
Do you want to optimize your production with industrial automation?
Contact Ercopac for a personalized consultation.
General questions about industrial robotics:
- Q: What is the difference between a traditional industrial robot and a cobot?
- Traditional industrial robots are designed for repetitive tasks and operate in isolated areas for safety reasons. Cobots, or collaborative robots, are designed to work alongside humans in shared spaces with advanced safety sensors.
- Traditional industrial robots are designed for repetitive tasks and operate in isolated areas for safety reasons. Cobots, or collaborative robots, are designed to work alongside humans in shared spaces with advanced safety sensors.
- Q: What are the main areas where industrial robotics is most used?
- Major sectors include automotive, food, logistics, pharmaceuticals, electronics, and general manufacturing.
- Major sectors include automotive, food, logistics, pharmaceuticals, electronics, and general manufacturing.
- Q: How is artificial intelligence affecting industrial robotics?
- AI enables robots to make more complex decisions, adapt to unexpected situations, learn from experience and optimize processes in real time.
Questions on Implementation and Costs:
- Q: What is the average cost of implementing a robotic system?
- The cost varies widely depending on the complexity of the system, type of robot, accessories, and software. However, it is important to consider the long-term ROI, which often offsets the initial investment.
- The cost varies widely depending on the complexity of the system, type of robot, accessories, and software. However, it is important to consider the long-term ROI, which often offsets the initial investment.
- Q: What are the factors to consider before investing in industrial robotics?
- It is critical to assess the specific needs of the company, the processes to be automated, the expected ROI, staff training, and integration with existing systems.
- It is critical to assess the specific needs of the company, the processes to be automated, the expected ROI, staff training, and integration with existing systems.
- Q: How long does it take to integrate a robotic system into an existing production line?
- Integration time depends on the complexity of the system and the readiness of the company. Typically, it can range from a few weeks to several months.
Labor Impact Questions:
- Q: Will industrial robotics lead to job losses?
- Robotics will transform the job market, eliminating some repetitive tasks but creating new opportunities in roles supervising, programming and maintaining robots.
- Robotics will transform the job market, eliminating some repetitive tasks but creating new opportunities in roles supervising, programming and maintaining robots.
- Q: What skills will be needed to work with industrial robots?
- Skills in programming, maintenance, robotics, AI, data analysis, and automated systems management will be required.
- Skills in programming, maintenance, robotics, AI, data analysis, and automated systems management will be required.
- Q: How can companies prepare their employees for the transition to automation?
- Companies should invest in training and retraining programs, offering employees the opportunity to acquire new skills.
Sustainability Questions:
- Q: How can industrial robotics contribute to environmental sustainability?
- Robotics can optimize production processes, reduce material and energy waste, improve waste management and promote a more circular economy.
- Robotics can optimize production processes, reduce material and energy waste, improve waste management and promote a more circular economy.
- Q: What are the most sustainable robotic technologies?
- Cobots, autonomous mobile robots (AMRs) and machine vision systems can help reduce environmental impact through their energy efficiency and ability to optimize processes