Industry 5.0 marks a paradigm shift in the manufacturing sector, bringing with it a more harmonious interaction between automation, artificial intelligence and the human operator. This concept goes beyond the digitization driven by Industry 4.0 to create smart, safe and sustainable manufacturing environments.
One of the pillars of this evolution is the adoption of AGVs (Automated Guided Vehicles) and LGVs (Laser Guided Vehicles) with autonomous navigation in unstructured environments through the integration of artificial intelligence, advanced sensors and machine learning.
But what makes these vehicles a revolution in industrial logistics? And how can companies take full advantage of their implementation? In this article, Ercopac analyzes the new technologies that are redefining the concept of mobile automation and their integration into modern production processes.
Industry 5.0: A new balance between man and machine
Unlike Industry 4.0, which focused on automation and digital interconnection, Industry 5.0 places the human being at the center of technological transformation.
This means that new technologies, such as smart AGV-LGVs, do not replace human labor, but optimize its efficiency, improve safety and ensure greater sustainability of industrial processes.
Artificial intelligence plays a key role in this evolution, enabling autonomous vehicles to dynamically adapt to the environment, improving operational flexibility and reducing cargo handling times.
Natural autonomous navigation: how it works and why it is a revolution
Traditional AGV-LGVs required physical guides, such as magnetic strips or floor sensors, to follow a predefined path. Thanks to natural autonomous navigation, today these systems can move through unstructured environments without the use of fixed infrastructure. But how is this possible?
Key technologies of autonomous navigation
- LiDAR (Light Detection and Ranging) sensors → They create a three-dimensional map of the surrounding space, allowing detection of obstacles and optimal paths.
- Artificial vision → Using stereoscopic cameras and depth sensors, the vehicle can recognize and classify objects, people and signals.
- Machine Learning and AI → The algorithm learns from the collected data and continuously optimizes navigation, making the system increasingly intelligent and adaptive.
- IoT and Cloud Integration → Vehicles communicate with the enterprise infrastructure in real time, optimizing logistics and production flows.
Concrete benefits:
- Total flexibility: routes are adjusted in real time without the need for manual reconfiguration.
- Reduced handling time: AGV-LGVs independently find the most efficient route.
- Advanced safety: recognition systems avoid collisions and operate safely with operators.
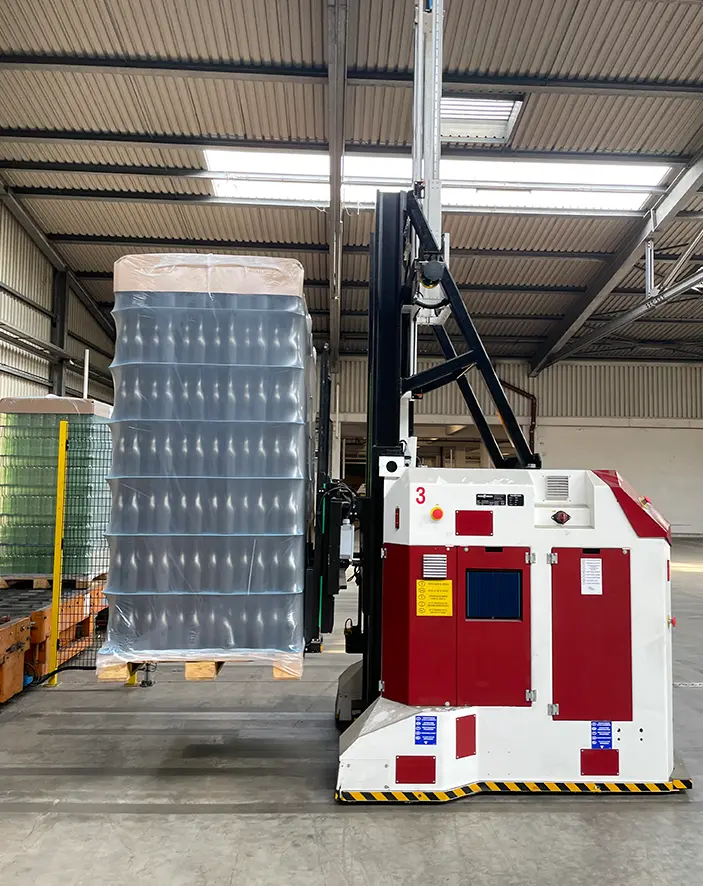
The integration of AGV-LGVs in companies: benefits and use cases
The implementation of AGV-LGV brings benefits in several areas, including:
- Logistics and warehousing → Optimization of materials management with reduction of transportation time by 30%.
- Automotive and manufacturing → Automation of component handling in assembly lines.
- Food & Beverage → Intelligent transportation of raw materials and finished products, meeting strict food safety standards.
- Pharmaceutical and cosmetics → Reducing errors in distribution with advanced batch traceability.
- Paper and tissue → Automated pallet handling to optimize the continuous flow of high-turnover products and minimize the risk of damage.
Ercopac responds to the challenges of intralogistics automation with ErcoMove, the new range of AGVs and LGVs designed to ensure maximum safety, operational precision and logistical flexibility. Equipped with anti-collision sensors, visual and audible alerts, and mechanical protection systems, ErcoMove vehicles operate in full harmony even in complex production environments shared with operators.
Each vehicle is natively integrated with Ercopac’s end-of-line systems, communicating in real time with PLCs and management software to ensure total synchronization with production flows. Routes are easily reconfigurable so they can adapt to new requirements, variable layouts or seasonal peaks.
Fluid Manager software completes the ecosystem, offering a centralized management system based on the standardized VDA 5050 protocol, which allows the integration of AGVs and AMRs from different manufacturers. With its predictive simulation module and patented Zero Deadlock algorithm, bottlenecks can be eliminated, business continuity ensured, and downtime drastically reduced.
Advanced solutions for autonomous movement: ErcoMove and Fluid Manager
Ercopac responds to the challenges of intralogistics automation with ErcoMove, the new range of AGVs and LGVs designed to ensure maximum safety, operational precision and logistical flexibility. Equipped with anti-collision sensors, visual and audible alerts, and mechanical protection systems, ErcoMove vehicles operate in full harmony even in complex production environments shared with operators.
Each vehicle is natively integrated with Ercopac’s end-of-line systems, communicating in real time with PLCs and management software to ensure total synchronization with production flows. Routes are easily reconfigurable so they can adapt to new requirements, variable layouts or seasonal peaks.
Fluid Manager software completes the ecosystem, offering a centralized management system based on the standardized VDA 5050 protocol, which allows the integration of AGVs and AMRs from different manufacturers. With its predictive simulation module and patented Zero Deadlock algorithm, bottlenecks can be eliminated, business continuity ensured, and downtime drastically reduced.
In summary, ErcoMove and Fluid Manager represent a scalable, interoperable and highly adaptable solution designed for the future of intelligent intralogistics.
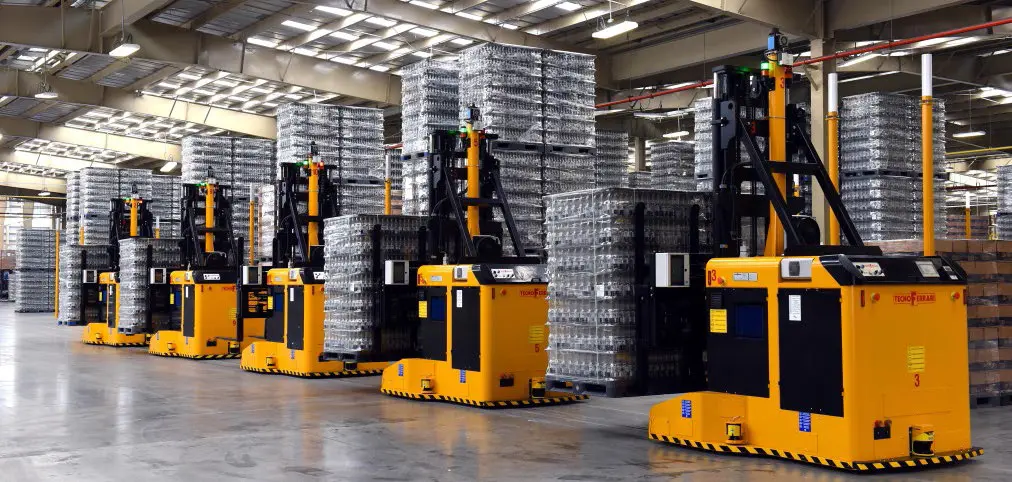
Industry 5.0 is already a reality
The use of intelligent AGV-LGVs is no longer a future possibility, but a reality for many companies that focus on efficiency, safety and sustainability.
Industry 5.0 is transforming manufacturing, puttinghuman beings at the center of innovation and using technology as a strategic ally.
Ercopac supports companies in the transition to intelligent robotics. Discover our solutions for industrial automation.
General questions about Industry 5.0 and autonomous navigation
What is the main difference between Industry 4.0 and Industry 5.0?
Industry 4.0 focuses on digitization and process automation, while Industry 5.0 emphasizes human-machine collaboration, customization and sustainability.
What is meant by “natural autonomous navigation”?
It refers to the ability of mobile robots (such as AGV-LGVs) to move in unstructured environments without the aid of physical guides (tracks, magnets), using sensors and AI algorithms to orient themselves.
In what types of industrial environments is autonomous navigation most beneficial?
It is especially useful in dynamic and fast-changing environments, such as warehouses, distribution centers and flexible manufacturing facilities.
Technical Questions on AGV-LGVs and AI:
What are the advantages of using LiDAR sensors and 3D cameras in AGV-LGVs?
These sensors enable robots to create detailed maps of their surroundings, detect obstacles, and plan optimal routes in real time.
How do machine learning algorithms improve the performance of AGV-LGVs?
They enable robots to learn from experience, adapt to unexpected situations, optimize routes and improve navigation accuracy.
How is the safety of human operators working alongside AGV-LGVs ensured?
The robots are equipped with advanced safety sensors, obstacle detection systems and algorithms that enable them to slow down or stop in the event of
danger.
Questions on Implementation and Benefits:
What are the main advantages of integrating intelligent AGV-LGVs into production systems?
Optimizing workflows, reducing transportation time, improving safety, reducing operational costs, and improving sustainability.
What are the factors to consider before implementing an AGV-LGV system with autonomous navigation?
It is critical to assess the specific needs of the company, the configuration of the work environment, integration with existing systems, and staff training.
How can the implementation of AGV-LGV contribute to environmental sustainability?
Reducing energy consumption, decreasing CO2 emissions and optimizing resource management.
Questions on the Future of Mobile Robotics:
What are the next expected developments for AGV-LGVs?
Increased integration with collaborative robotics, improvements in computer vision, and greater connectivity with IoT networks.
How can companies prepare for the adoption of advanced mobile robotics technologies?
Investing in staff training and retraining, collaborating with technology solution providers, and taking a phased approach to implementation.