In the packaging industry, quality is not just an added value, but a fundamental requirement to ensure product safety and end customer satisfaction. The increasing complexity of production lines requires solutions that go beyond simple visual inspection, integrating advanced technologies for systematic and automated verification.
Ercopac stands out for its ability to innovate in this area, offering quality control systems patented that ensure the highest level of reliability and precision.
An advanced system for real-time monitoring
Ercopac ‘s innovative quality control system integrates in-line wrapping tests and pallet compliance verification tools, enabling continuous , real-time monitoring .
This technology makes it possible to:
- Detect defects immediately: Any abnormalities in the loads, pallets or wrapping film are detected promptly.
- Prevent waste: The ability to take immediate action reduces waste and optimizes the use of materials.
- Ensuring compliance: Each pallet undergoes audits that certify its safety and stability, ensuring that the required standards are met
With this system, companies can rely on dynamic and reliable quality control that minimizes the risk of errors and inefficiencies.
Operator Safety in Empty Pallet Control.
Operator safety is a top priority in the empty pallet control systems developed by Ercopac. The technologies implemented are designed not only to minimize the risks associated with manual handling of pallets, but also to prevent the dangers associated with the use of nonconforming pallets in the later stages of the production process.
In fact, a defective pallet can tip over during handling, potentially injuring nearby operators, or compromise load stability during palletizing and wrapping, generating the risk of product spills and storage area contamination.
Through accurate and automatedcontrol, Ercopac systems ensure the compliance of pallets used on the line, making a major contribution to a safer and more secure working environment.
Key features of Ercopac systems include:
- Full automation of inspections: The system, based on the use of robots, allows for full automation of inspections on empty pallets, avoiding any manual intervention by operators in the picking and depositing phases. This approach not only optimizes time and reduces handling risks, but also ensures maximum reliability of the inspection process, ensuring efficient handling even in the presence of nonconforming pallets.
- Advanced warning systems: Sensors and alarm devices detect anomalies in the pallets, alerting the operator only when necessary, avoiding unnecessary risk exposure.
- Ergonomic design: The control and intervention stations are designed to minimize physical strain on operators, preventing accidents and injuries from repetitive strain. In addition, the entire system is designed to be highly accessible and requires little maintenance, thanks to the use of robotics, which has made it possible to minimize mechanical components.
- Protection during discarding: Nonconforming pallets are automatically discarded and conveyed to safe areas, without the need for direct handling by operators.
Through these measures, Ercopac’s empty pallet control systems not only ensure high operational accuracy, but also provide a higher level of safety for operators, helping to create a more protected and productive work environment.
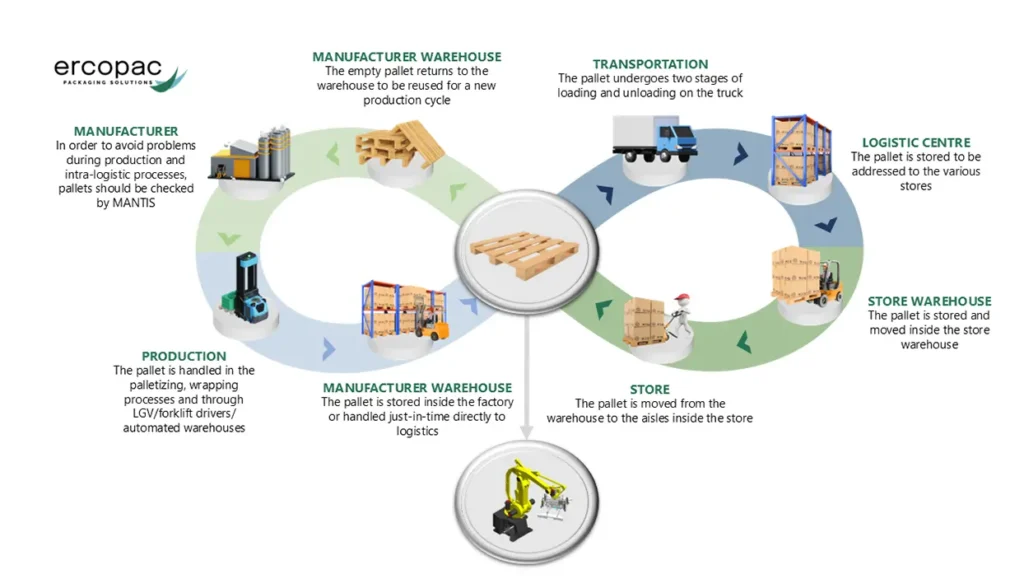
The automated system MANTIS for checking empty pallets represents one of the most advanced solutions developed by Ercopac in safety and automation. As shown in the schematic, each pallet goes through a sequence of dedicated stations that check for structural integrity, the presence of defects (such as dangling axles or damaged plinths) and the correct configuration for use in subsequent processes.
Thanks to robotic management, MANTIS ensures a continuous and reliable flow: conforming pallets are automatically routed to the operating area, while non-conforming pallets are safely diverted to a dedicated rejection station, reducing the risk of human error and improving overall process quality.
Learn more about MANTIS technology
Patented technology for palletized load stability
The heart of Ercopac’s innovation lies in its patented system for verifying the stability of the palletized load.
Through advanced sensors and algorithms, the technology analyzes key parameters such as:
- Stretch film tension
- Adhesion of layers
- Resistance to movement during transport
This scientific approach to stability not only ensures uniform and safe wrapping, but also optimizes film consumption, improving the sustainability of the production process.
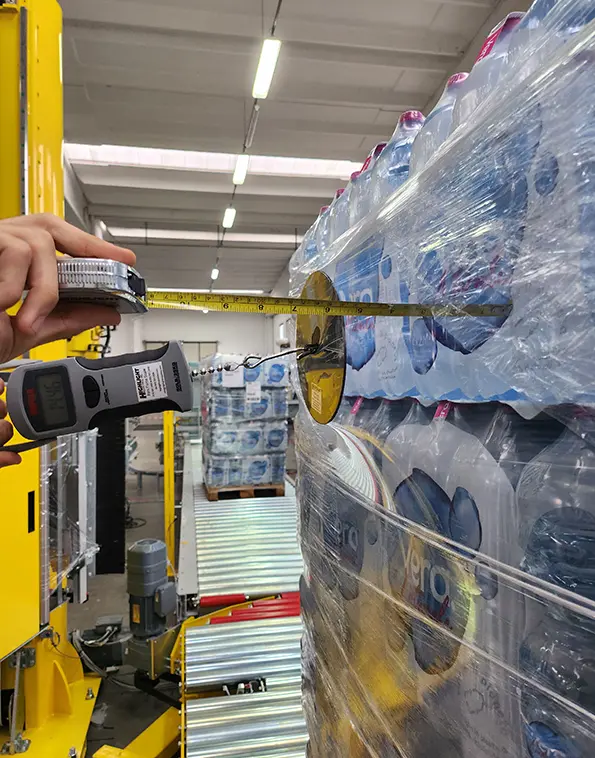
Modularity: adapt to each production line
A distinctive feature of Ercopac quality control systems is their modularity, which allows easy integration into existing or new production lines. This flexibility enables companies to adapt quickly to market changes without disrupting production.
Modularity translates into:
- Cost reduction: A single system can be used for different production configurations.
- Operational simplicity: Scalability ensures rapid implementation without complexity.
- Future-proofing: Modular solutions are easily upgradable to include new technologies.
Benefits for the end customer
High-quality packaging is not only an advantage for the manufacturer, but also a guarantee for the end customer.
Strict quality control:
- Protects product integrity: Prevents damage during transport or storage.
- It increases customer satisfaction: A well-packaged product conveys professionalism and care.
- Reduces complaints: Compliance with technical and regulatory requirements minimizes the risk of complaints.
Ercopac’s role as a strategic partner
With its experience and continuous innovation, Ercopac is a benchmark for companies seeking advanced solutions for quality control in packaging. The combination of patented technologies, modular systems anddedicated technical support makes Ercopac a reliable partner for meeting quality challenges in an ever-changing market.
Investing in an effective quality control system is not only a strategic choice, but a necessity to compete in the demanding packaging industry. With Ercopac, companies can count on solutions that combine precision, flexibility and sustainability, ensuring the highest quality products and optimal resource management.
Why is quality control in packaging important?
Quality control is critical for several reasons:
- Product safety: Prevents contamination, damage and alterations that could compromise consumer health (especially in the food and pharmaceutical sectors).
- Product integrity: Ensures that the product reaches the consumer in optimal condition, preserving its quality characteristics.
- Regulatory Compliance: Ensures compliance with laws and industry standards (e.g., food packaging regulations, pharmaceuticals, etc.).
- Customer satisfaction: Integral and functional packaging contributes to a positive consumer experience.
- Brand Reputation: Defective packaging can damage corporate image and consumer trust.
- Reducing waste and returns: Effective control prevents defects that would lead to production waste or customer returns.
What are the main types of tests that are carried out on packaging?
There are different types of tests, depending on the type of packaging and the product contained:
- Mechanical strength test: They test compressive, tensile, impact, puncture resistance, etc.
- Leak test: They test sealing ability and protection from external agents (moisture, oxygen, etc.).
- Migration testing: They test the release of substances from the packaging to the product.
- Compatibility tests: They test the interaction between the packaging and the product.
- Visual tests: They check the aesthetic integrity of the packaging (printing defects, labeling, etc.).
- Cargo stability tests: check the stability of palletized and wrapped cargo before it is transported or stored
What are the reference standards for quality control in packaging?
Regulations vary by industry. Some examples include:
- European regulations on food contact materials (e.g. EC Reg. 1935/2004 and EC Reg. 2023/2006).
- ISO standards (e.g., ISO 22000 for food safety, ISO 9001 for quality).
- Good Manufacturing Practices (GMP) guidelines for the pharmaceutical industry.
- Specific regulations for the transport of dangerous goods (ADR).
What are the consequences of defective packaging?
The consequences can be many:
- Product contamination: Health risk to consumers.
- Product Deterioration: Loss of quality and commercial value.
- Customer returns and complaints: Additional costs to the company and damage to image.
- Legal Penalties: In case of non-compliance with regulations.
- Damage to corporate reputation: Loss of consumer trust.
How is quality control integrated with other stages of the production process?
Quality control should be integrated into all stages of the process, from packaging design to production, packaging, storage and transportation. This approach, called “total quality,” allows defects to be prevented rather than corrected after the fact.
How does the system for verifying the stability of paddles work?
The automatic pallet control system ensures-through careful preliminary selection-theuse of pallets that conform to customer requirements and theelimination of those that do not.
The system is structured in several stations that the empty pallet passes through to be controlled. One of the main advantages of using the robot is that already during picking and before depositing, a series of checks are made; this implies that, in case of nonconformity, the pallet automatically goes to the reject station, and otherwise continues on the control path.
If it has no defects, it is placed in the good paddle stack station (divided into 2/3 different types), otherwise on the stack station discarded pallets. It is rare that the pallet in this cycle can get stuck.
The main checks that are carried out are: integrity of plinths, protruding nails, strength of lower and upper axles, leaning axle, and forking compartments.
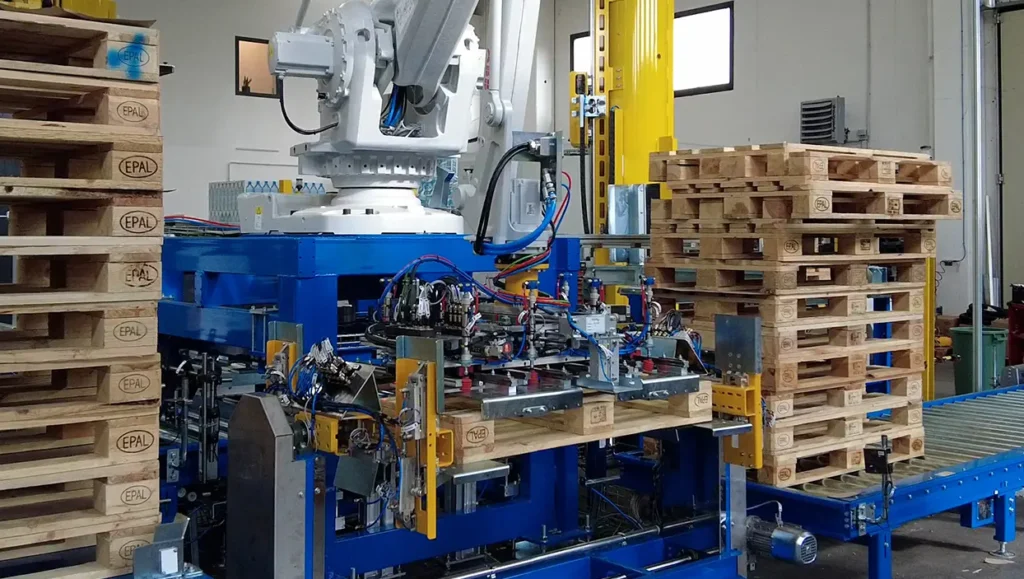
What parameters are measured by Ercopac’s system?
The in-line wrapping test station (patented by Ercopac) is designed to simulate the conditions that a pallet load, already wrapped with protective film, might face during transport and storage. In practice, it is used to see if the wrapping holds up well even when the load is subjected to jolts, tilts or bumps, as happens on trucks, ships or other vehicles.
The system includes a platform that can tilt in different directions: either along the direction in which the load “travels” (forward and backward) or laterally. This causes the pallet to be exposed to forces similar to real ones caused by braking, cornering or sudden movements, testing the strength of the packaging.
A great advantage of this station is that it also allows manual testing. That is, an operator can intervene directly to do hands-on testing on the load, using instruments that are already approved and in line with industry standards.
To make the test even more realistic, the station also has blocks-one in front and one on the side-that serve to stop the pallet as it moves. When the load hits these blocks, an impact is generated that can deform it or make it move. This helps to see if the protective film has been applied in the right way, that is, if it can hold the various layers of the load in place without causing them to sag or shift.
Finally, there are also sensors that monitor the shape and size of the pallet before, during, or after the test. These instruments compare the sensed data with previously stored data to see if there are variations beyond acceptable limits based on the type of pallet.
In summary, this station is used to check how stable and secure a pallet-wrapped cargo is before it is actually shipped, thus helping to prevent damage and ensure safer and more efficient transportation.
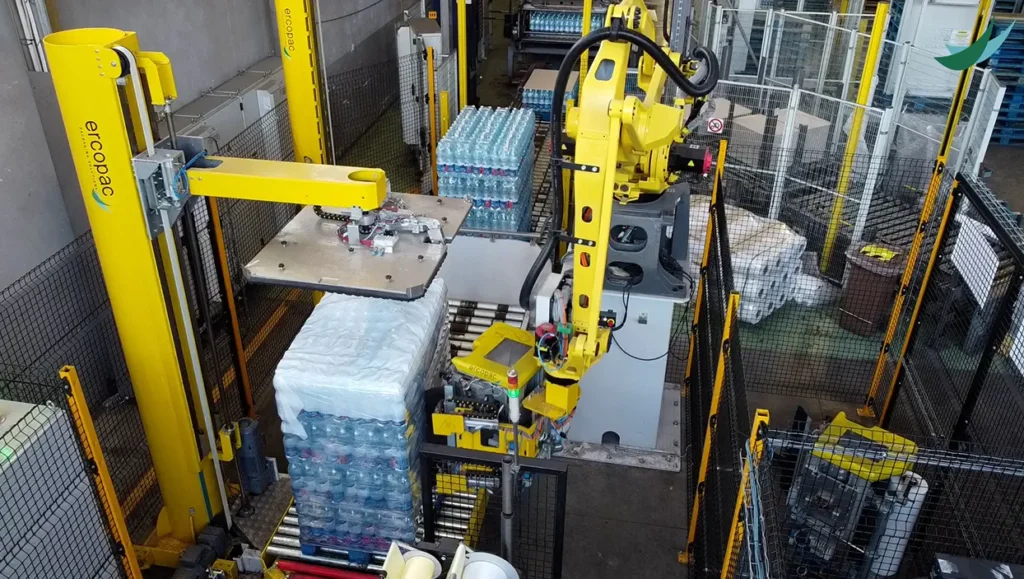
What are the specific advantages of Ercopac’s real-time monitoring system?
Ercopac’s real-time monitoring system offers significant advantages that improve the efficiency and accuracy of production processes.Prominent among these are theimmediate detection of defects, enabling timely action to resolve any problems, and the prevention of waste, reducing excessive consumption of materials. In addition, the system ensures compliance with quality standards, minimizing the risk of errors and inefficiencies.
An additional strength is theprogrammable control unit, which analyzes the results of the tests performed and converts them into operating instructions. These instructions are automatically sent to the wrapping station, optimizing or adapting the type of wrapping required to ensure optimal operation at all times. This combination of precision and automation enables companies to achieve high standards of quality and productivity.
Is Ercopac’s system suitable for all types of pallets and loads?
Ercopac ‘s systems are designed for maximum versatility and adaptability to different types of pallets and loads. In terms of pallet control, compatible formats include:
- EURO Pallet
- Half Pallet
- GMA Pallet
- CHEP Pallets
- CHEP Half Pallet
- Dusseldorf Pallet
On the wrapping test front, however, Ercopac systems accommodate a wide range of loads, such as bottles, bricks, cans , and paper rolls. These loads can be contained in different configurations, including cartons, bundles, bags and trays, always ensuring optimal stability and safety during storage and transport.
Ercopac offers technical support and maintenance for its systems?
Ercopac provides comprehensive technical support and maintenanceservices designed to meet the specific needs of each customer. The offering includes scheduled and unscheduled maintenance, ensuring that systems always operate at peak performance. On-site interventions are accompanied by detailed reports and updates to the operating and maintenance manual, providing customers with all the information they need for optimal management.
To support operational efficiency, Ercopac also offers customized training courses, available both online and on-site, with evaluation tests to ensure a thorough understanding of the implemented technologies. Content and delivery methods are adaptable to specific needs, agreed directly with the customer.
Finally,technical support is available both remotely and on-site, with advanced diagnostic services to resolve hardware and software issues. This integrated approach keeps systems running smoothly, reducing downtime and ensuring continuous and reliable support.
Impact on Product Safety and Quality:
Packaging quality control plays a key role in ensuring the safety and preservation of products. Proper packaging protects contents from external agents such as oxygen, moisture, light, and microorganisms, slowing deterioration and helping to extend shelf-life. However, defective packaging can have serious consequences, allowing contamination by bacteria, mold or harmful substances, posing significant health risks to consumers.
In addition to protection, quality control also helps to prevent counterfeiting through the implementation of security elements such as holograms, microprinting, special inks and traceability systems. These tools offer greater assurance of authenticity and transparency throughout the supply chain.
Best practices for packaging quality control vary by industry, but include strict adherence to specific regulations, validation of packaging processes, constant monitoring of critical parameters, ongoing staff training, anduse of advanced technologies. These approaches ensure high standards in the most critical sectors, such as pharmaceutical, food and industrial, where packaging quality is closely linked to safety and end customer satisfaction.